Introduction to eECD
![]() | An ECD (EFTCO Cleaning Document) is a support document for every single tank cleaning in the supply chain process. Advantages of an ECD are:
It supports the Responsible Care program of the chemical Industry (Cefic). The project objective of the eECD use case is to digitize the ECD, supported by ECLIC, EFTCO, ECTA, Cefic-essenscia and the NxtPort data platform. This article describes the different process steps supported by the eECD digitization project. |
---|
Introduction Video
Stakeholders
Within a typical cleaning in the Chemical industry, different parties communicate in order to request transport orders and linked Cleanings. We identified the following stakeholders each with a certain responsibility. A company can have different roles in the setup. E.g. a Seller will often be a Loader; an equipment operator can also handle his own cleanings, etc.
Seller
The organization or legal entity which sells the product to the customer and instructs the transfer of goods by initiating the transport order. This is typically the ChemCo but can also be a ReSeller who resells the ChemCo’s product under its own trade name.
The Seller defines the commercial or trade name of the products sold. The Seller owns the product registrations and is responsible for the product master data while providing the right Safety data information. If the seller is not yet fully integrated, he also maintains a list of permitted loading locations per product.
Equipment operator
The organization or legal entity which is the operator of the equipment and performs the actual transport of the goods. This is typically a TransCo, but it might be a ChemCo/Seller who operates his own dedicated tank fleet. In the typical flow, the EquipmentOperator receives the transport order from the Seller and issues a cleaning request to the Cleaner. In addition, The EquipmentOperator assigns the right equipment to a transport order reference and add the products and loading information for the goods to be loaded if required.
The EquipmentOperator is responsible to maintain the equipment master data. Besides the EquipmentOperator is responsible to add/share the previous load information with the cleaning station prior a cleaning starts.
The truck driver signs off the digital eECD on glass for acceptance of the cleaning service at the cleaning station.
Cleaner
The organization or legal entity which performs the equipment cleaning activities as per cleaning instruction provided by the EquipmentOperator. This is a CleanCo.
The Cleaner is responsible for the definition of cleaning locations within the cleaning organization while assigning cleaning operator/users to these cleaning locations.
Loader
The organization or legal entity which manages the loading of the goods . This can be the ChemCo, a tank storage operator company or a third party producing tolling agent. This role confirms the products being loaded per equipment compartment.
Process steps
eECD follows an "agile project approach" allowing to shape the solution while rolling it out in short (monthly) releases and feedback loops. We focus on added value for active stakeholders, stable (yet quick) deliverables and proactive (re)design.
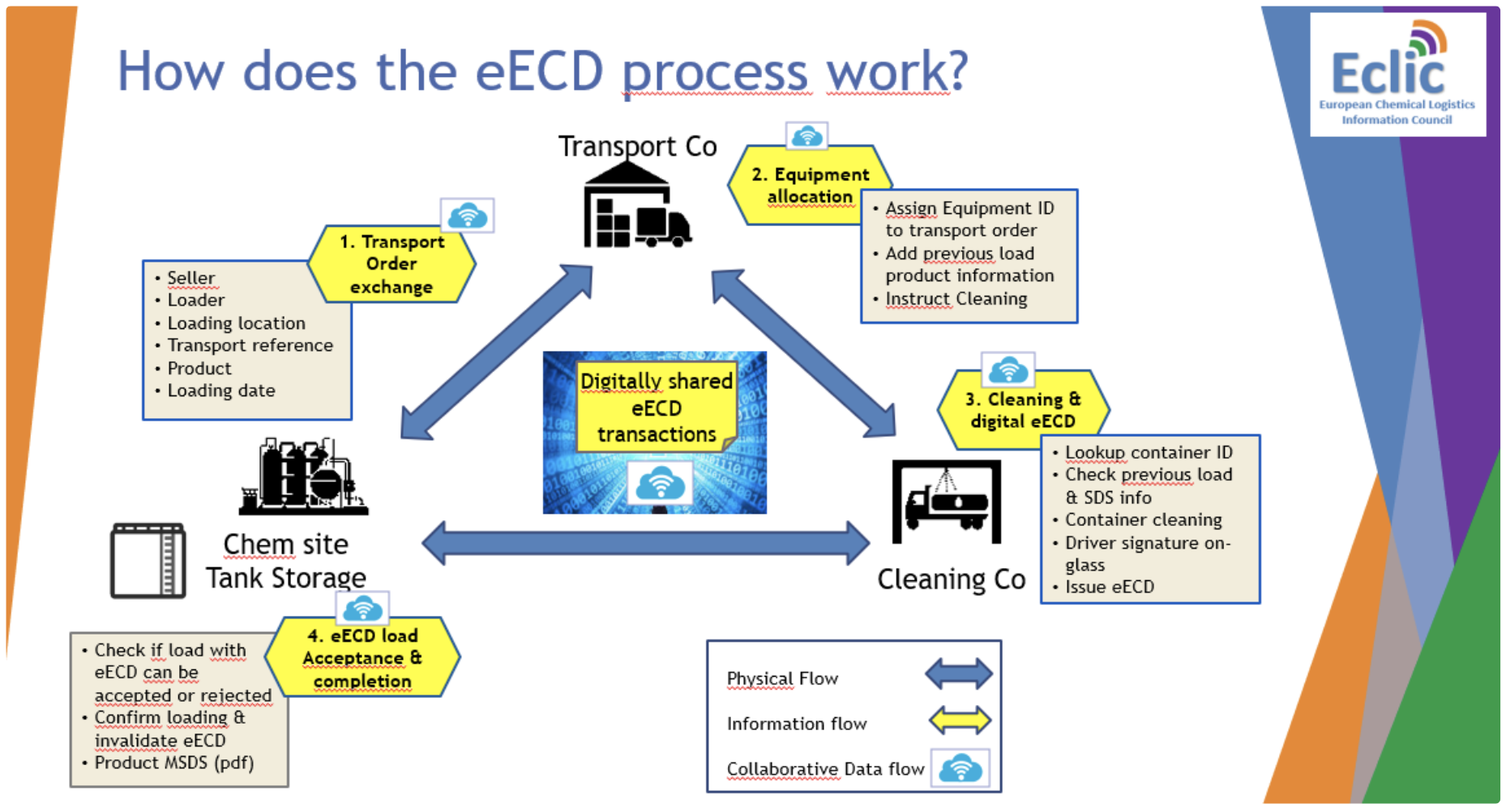
Building block | Estimated delivery dates | Most used functionality (technical) | |
---|---|---|---|
1 | Send or exchange transport orderThe Seller sends a transport order towards an EquipmentOperator by EDI, fax, email,.... The transport order info typically consists of a set of parameters:
Available integrations - avoiding to retype transport order info Existing transport order exchange methods already in place with Elemica, Transwide,...can be simply re-used. A standard eECD transport order data subset and format is made available via Elemica / Transwide and can send the required transport order information digitally towards the ECLIC platform and this to avoid information needs to be entered manually. Other software interfaces are being set up. | Current status LIVE Available
| Get all transport orders
eECD standard transport data subset exists. Integrated Seller set up |
2 | Assign equipment to transport order and loaderBased upon the transport plan, the EquipmentOperator assigns an equipment ID (e.g. a tankcontainer ref nr.) to the transport order reference taking into account the previous product load info. This equipment assignment can happen before or after the cleaning action and is done per equipment compartment. The cleaning status per equipment compartment is made visible to the equipment operator. In case the previous load info is missing - for instance when a new tankcontainer is used for the first time within the digital eECD process - the EquipmentOperator adds the missing previous load info by creating a "Non-Registered Load" product record and can add any attachments (eg CMR with proof of previous load or SDS info sheet). Furthermore, the EquipmentOperator selects the product and loading info in case of manual way of working. In case of the integrated work method by the Seller described above, the product and load info is already pre-filled by selecting the right transport order reference. | Current status LIVE Available
| Create equipment Search for products Assign a load to an equipment |
3 | Send cleaning an electronic EFTCO cleaning order instructionThe equipment operator sends an electronic EFTCO cleaning order for an equipment ID towards a cleaning station. The cleaning station is able to accept or reject this cleaning order. Remark | Current status LIVE Available |
|
4 | Start cleaningIn case there is no cleaning order instruction, the digital cleaning process starts with an empty and unclean container arriving at the cleaning station. This we call a cleaning request. At the check in, the cleaning operator selects within the eECD application first the right EquipmentOperator and subsequently the correct equipment ID and obtains a list of all potential equipment choices. Both parameters, EquipmentOperator and equipment ID are required an equipment ID is found and before the eECD booklet can be opened to check the equipment configuration & cleaning details. In case the right container is displayed the operator can push the "start cleaning" button. Subsequently the cleaning station, and some cleaning options like "unaccompanied cleaning and polymer cleaning" can be ticked before the cleaning itself begins (=button begin cleaning). Once "begin cleaning" button is pressed, the eECD document details can be further completed by equipment compartment and saved till the cleaning is ready for eECD signoff. Besides, the previous load product info can be digitally consulted by compartment within the eECD booklet history. Important is to ensure the cleaning "TIME IN " and cleaning TIME OUT fields are correctly completed with the correct date/time stamps before cleaner signoff. A digital cleaning can still be modified in case EFTCO cleaning instructions or comments should be added. In additions documents can be added to a cleaning as for instance pressure test results. A cleaning can also be cancelled after saving in case anyhow the customer would require a paper ECD. | Current status LIVE Available
| Start cleaning |
5 | Cleaner sign-offAfter performing the cleaning, the cleaner issues and signs off the eECD. The Cleaner can still invalidates the eECD in case anyhow the customer would require a paper ECD. | Current status LIVE Available
| Get a single cleaning action |
6 | Driver sign-offWhen picking up the cleaned equipment, The cleaning station can look up the eECD and the trucker driver signs-off the issued eECD at the cleaning station when the cleaning services are ok. After driver signoff the eECD status beomes SIGNEDOFF indicating that the equipment is now clean and ready to be used for a next loading. | Current status LIVE Available
| Open booklet of cleaning actions |
7 | Accept LoadWhen the equipment arrives at the site of the Loader, the Loader accepts (or rejects) the eECD based on the available information and a physical check. | Current status LIVE Available | Open booklet of cleaning actions |
8 | Complete LoadThe Loader loads the products into the cleaned equipment and this per compartment. Once the loading operator confirms the load, the equipment is no longer "clean" and the eECD certificate will no longer be valid for future usage, indicating that the process restarts once the products have been discharged at their destination. | Current status LIVE Available | Get a specified load |