Assign load
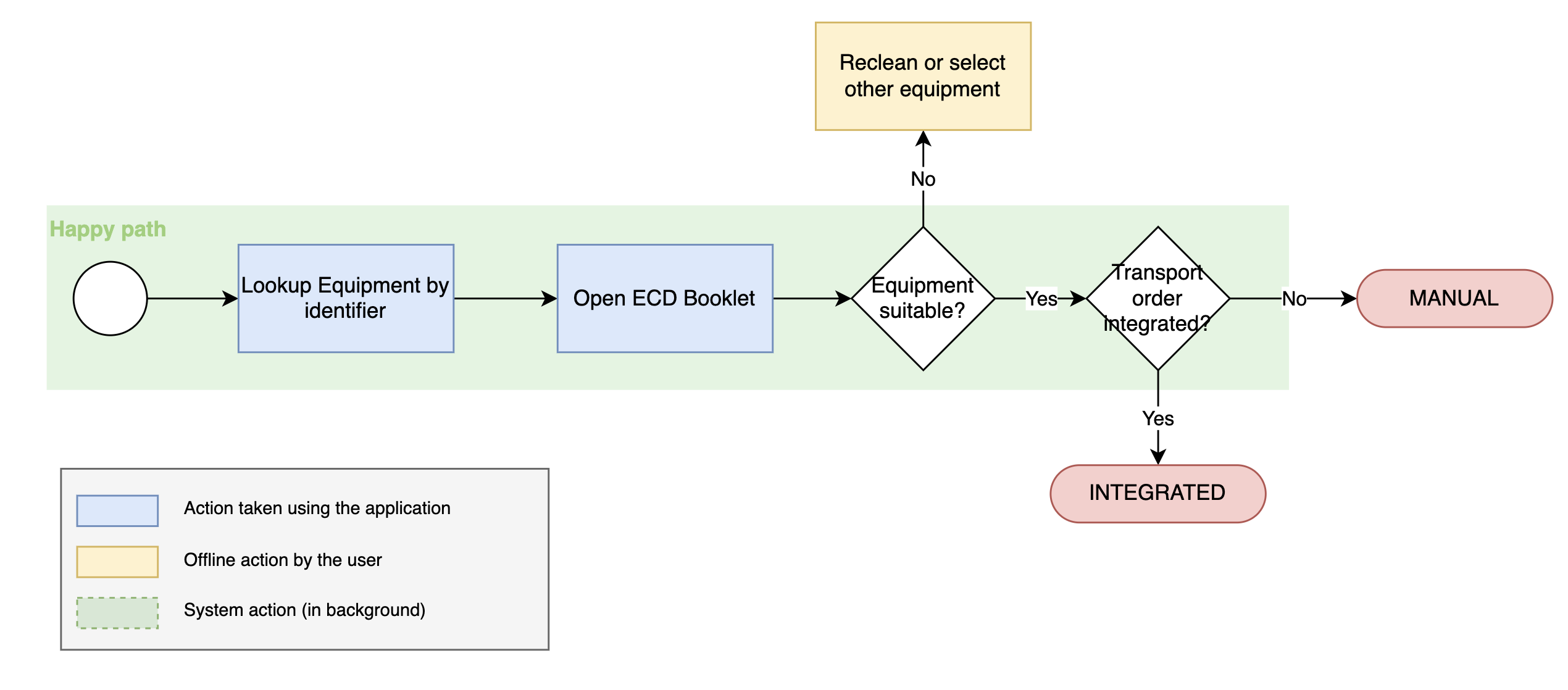
Italics indicates this happens at the despatcher discretion.
The despatcher already sent the required cleaning request and decides which uniqueEquipmentID he will select and use to fulfill transport order X
Verifies if equipment E can be used for this load
Checks product restrictions by Seller (forbidden preloads)
Checks if additional certificates needed
Checks equipment availability - capability …
Action | Comment |
Once the right equipment E has been found in his own TMS system, the EquipmentOperator despatcher logs in into eECD application |
|
Looks up equipment E and opens the eECD booklet by pressing “assign load “ button | Via the equipment search function (on equipment identifier) |
If current equipment is not yet clean and he wants to use E anyway, the dispatcher sends a cleaning request to a cleaning station | This means the process moves back to step A |
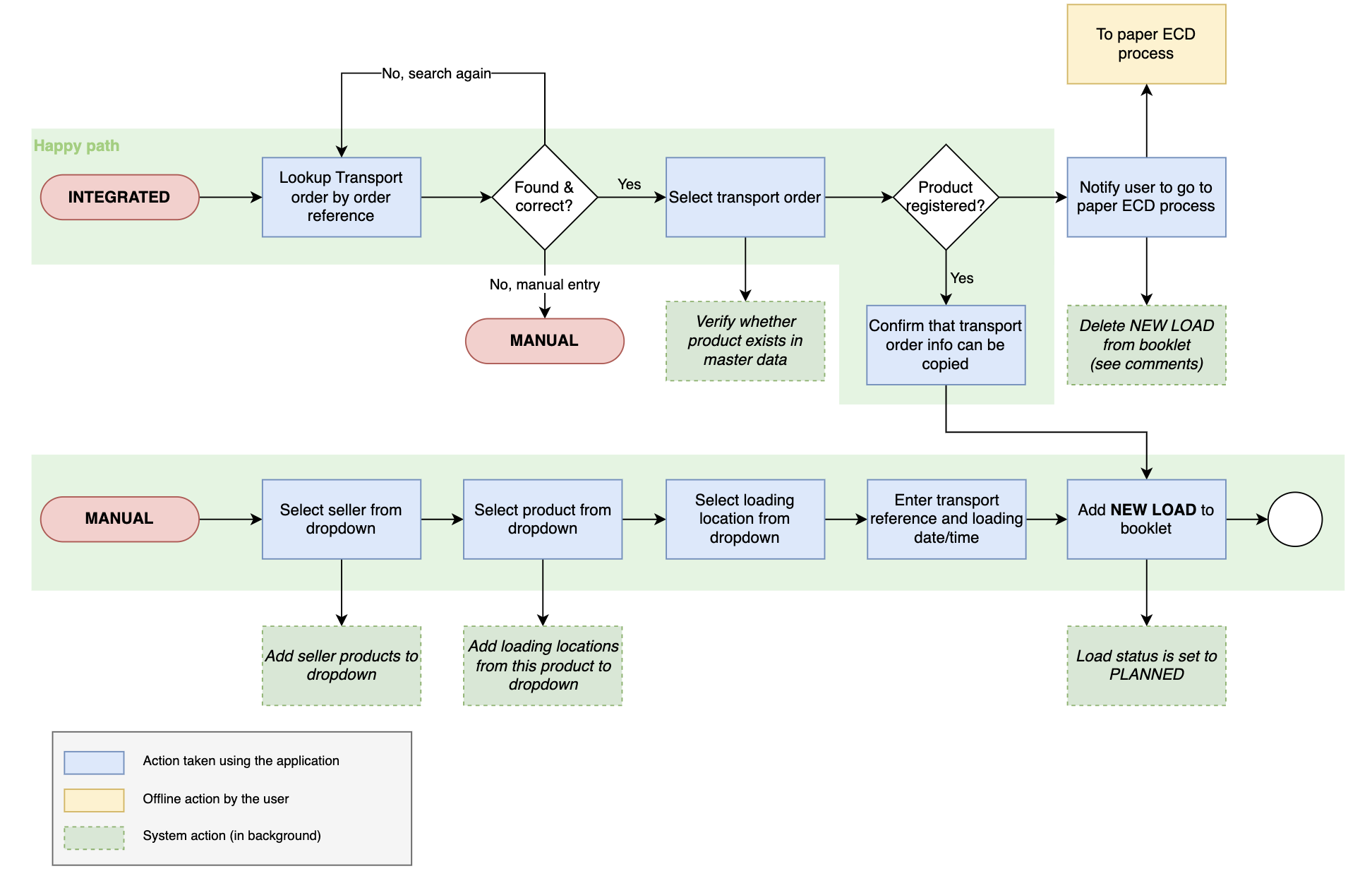
There are two ways to assign a load. Either the INTEGRATED way where the Seller has shared upfront the transport and product information with the ECLIC platform or either the MANUAL way where the Seller has provided the transport order info via EDI, email, fax, phone
If the EquipmentOperator has INTEGRATED their transport instructions (e.g. Via Elemica, Transwide or other)
|
|
If found
| Note: if article number is not present in the product master data list of the Seller
|
If no integration or no reference to supporting transport order found
| Automatic eECD validity expiry check: An ECD validity period can be added to the product master data . In such case, the ECLIC platform check the eECD date validity (ECD.date/time out + product-based expiration period <> planned load date) once the “product to load” has been assigned (warning only - product master data should contain max ECD validity) and generates a warning message. This expiry warning massage can be overruled by the loader or not. |
Loading locations
The loading location for a particular transport is not mentioned on the paper ECD and it has to be considered as supporting info to enable the digital eECD process. Loading locations are only known and identified in the eECD process as of when the “ship from” address from the transport order (for the next load) is provided through a supporting data connection. This “ship from” is a free text field in many legacy systems which means that only ‘simple & basic’ search functionalities are technically possible (for instance looking at the Company Name string “ADPO” in the ship from address and being “hardcoded with options (adpo, ADPO, Adpo, A.D.P.O. etc…”). To normalize these searches as best as we can, we allow sellers to define a set of permitted loading locations. Equipment operators will be able to select from a list of locations, reducing the number of mismatches.
The eECD project does not consider to setup a unique loading address codification system (e.g. unique EAN GTN numbering system) and prepare unique master data for all loading locations. The only purpose to add the loading partner is to ensure that only the right parties in the eECD information chain can consult information.
Different Loading locations per loader and per product can be uploaded by the Seller via a “loading location template or CSV file. In that case, the dispatcher gets a drop down list of potential loading locations to choose from and can select the one and mentioned on the transport order instruction. It is the responsibility of the Seller to provide the (latest) loading location info in a manual or automated way to third party service providers or to the ECLIC platform. In case of the INTEGRATED way of working the transport order info message has already shared this loading place info with the ECLIC platform and no manual entry by the despatcher is required when assigning the load.
It is recommended to set a ‘default loading location’ at the Seller level, to ensure that every product entry has at least one loading location.